Shelving Systems: Metro Shelving
Metro shelving is the most advanced and innovative wire storage system available. It is the easiest to adjust wire shelving system, adjusting space to meet your needs. Shelves have nickel-chrome plated finish. Durable and aesthetic for general applications.
An exceptionally strong, smart, and hard wearing wire shelving system, the open wire design promotes air flow. It is suitable for storage and display use in many industrial and commercial environments such as the electronics and pharmaceutical industries, catering and retail establishments, hotel, leisure, healthcare and hospital complexes.
Metro shelving is available in chrome, brite and stainless steel. Shelf styles include wire, solid, embossed and louvered embossed. A full choice of castor types are available as is a selection of shelf and post sizes.
Racking Systems: Pallet Racking: APR
Redirack Adjustable Pallet Racking is one of the most widely used systems for storing palletised unit loads. It consists of upright frames and horizontal beams that interlock to form the racking structure. Within the rack each pallet is individually accessible. Pallet Racking arranged in a wide aisle pattern requires no specialised handling equipment. Arranged this way it gives high quality storage but may only utilise 40% of the floor space. However, fast throughput and ease of loading and unloading make this type of storage extremely popular.
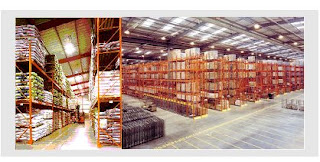
Racking Systems: Pallet Racking: Drive In
If storage capacity is a major requirement for a warehouse then drive-in racking is suitable. It eliminates aisles and lanes, resulting in a high storage density . But, the first pallet into a lane will be the last out. Still, if pallets are received and dispatched in batches this is not a disadvantage. Each pallet is supported so damage from crushing is eliminated.
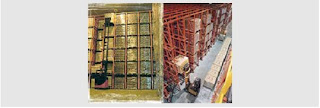
Racking Systems: Pallet Racking: Narrow-Aisle
Narrow aisle racking systems have aisles around 1.7 metres wide. It frees up to 45% for the floor space given over to aisles in a wide aisle scheme. The result is a significant increase in space utilisation. Each pallet is supported which means that stock rotation and accessibility is as good as a wide aisle system.
Racking Systems: Pallet Racking: Powered Mobile
Powered Mobile Racking consists of conventional pallet racking mounted upon a steel framed base. This has drive wheels which run on tracks in the floor. The system enables a run of racking to move to create an access aisle. Up to 80% of the floor area can be occupied for storage, while retaining access to every pallet. It has no bolts, thus it also eliminates the need for safety checks on the bolt for security of goods.
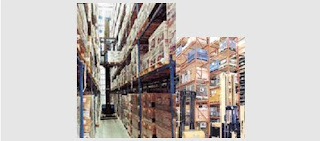
Racking Systems: Pallet Racking: Push Back
Push Back Racking is a form of pallet flow rack in which pallets are stored two, three or four deep with a telescopic trolley system. Using a fork lift truck, pallets are both loaded and unloaded from the same aisle. The palletised load is placed on the top trolley. When the next pallet is inserted this loaded trolley is pushed back into the storage lane. This process is repeated for up to four pallets deep. When a pallet is withdrawn from a lane, the remaining pallets stored behind are automatically fed forward under the force of gravity.
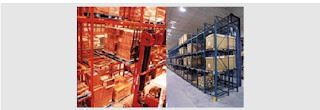
Racking Systems: Pallet Racking : Live Storage
Utilising gravity, live storage systems provide 'first in-first out' stock rotation, improved use of storage space and improved picking and loading speeds. The pallets rest on roller conveyor track and moves forward when a pallet is removed from the picking face at the front of the installation, creating a storage space on the loading face at the rear of the installation. Pallet live storage is used in conjunction with conventional counter balance or reach trucks.